Kingred Big Taper CNC Wire Cut EDM KD800W
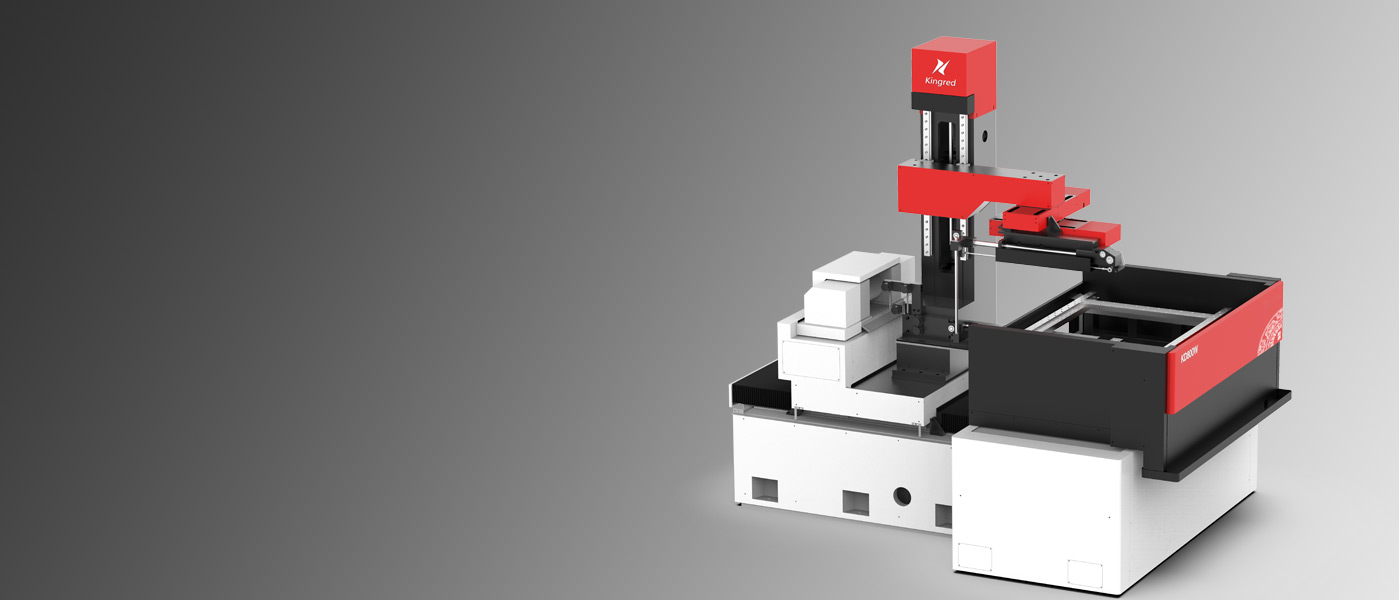
Unilateral max 30° taper machining.
Specially designed taper machining.
Y-axis flexible custom-manufacturing.
6-axis CNC.
Kingred Big Taper CNC Wire Cut EDM KD800W
Unit | Parameter | |
X*Y/ travel | mm | 630X800 |
U*V travel | mm | 280X280 |
Worktable size | mm | 770X1010 |
Machining parameters | ||
Cut accuracy straight/taper | mm | 土0.008/土0.025 |
Max cut taper | °/mm | 土30/80 |
Max cut speed | mm /min | 260 |
Max cut surface finish | μm | Ra≤1.0 |
Max cut current | A | 7 |
Max payload | kg | 2000 |
Max cut thickness | mm | 500 |
Min drive | mm | 0.001 |
Wire Parameters | ||
Diameter of wire | mm | Φ0.10-Φ0.25 |
Wire feed travel | mm | 280 |
Wire tightening type | CNC tighten wire | |
Max length of wire installed | m | 300 |
Basic parameters | ||
Rated power | kw | 3 |
Input voltage | V/Hz | 380/50 |
Weight of machine | kg | 7000 |
Outer size | m | 1.8*2.6*2.3 |
Packing size | m | 2.0*2.8*2.5 |
Tank parameters | ||
Capacity | L | 120 |
Filtering type | High pressure multi-stage filtration | |
Packing size | m | 0.7*0.7*0.8 |
Packing size | m | 0.9*0.9*0.9 |
G.M/N.M | kg | 80/60 |
1、 Big taper machining customization
Kingred specially designed big taper machining. Creative unilateral taper structure up to 30°
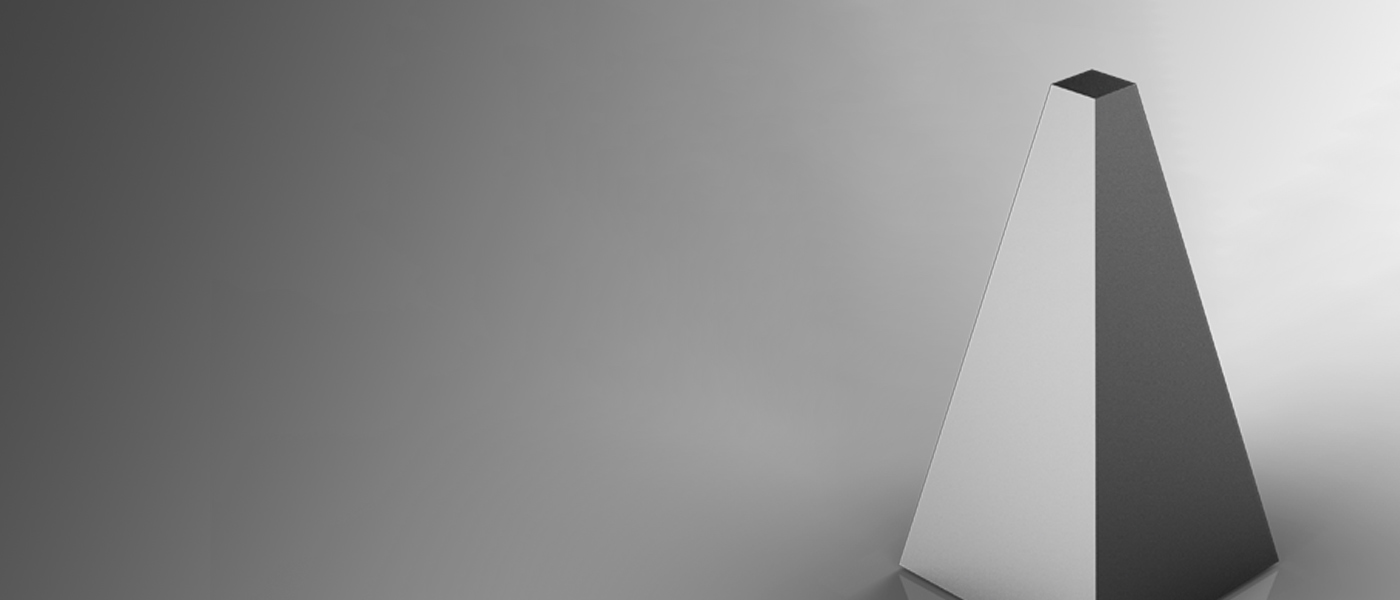
Kingred specially designed big taper machining. Creative unilateral taper structure up to 30°.
2、Specially designed taper structure
The up and down feed wire design of adjustable angle realized big taper cutting.
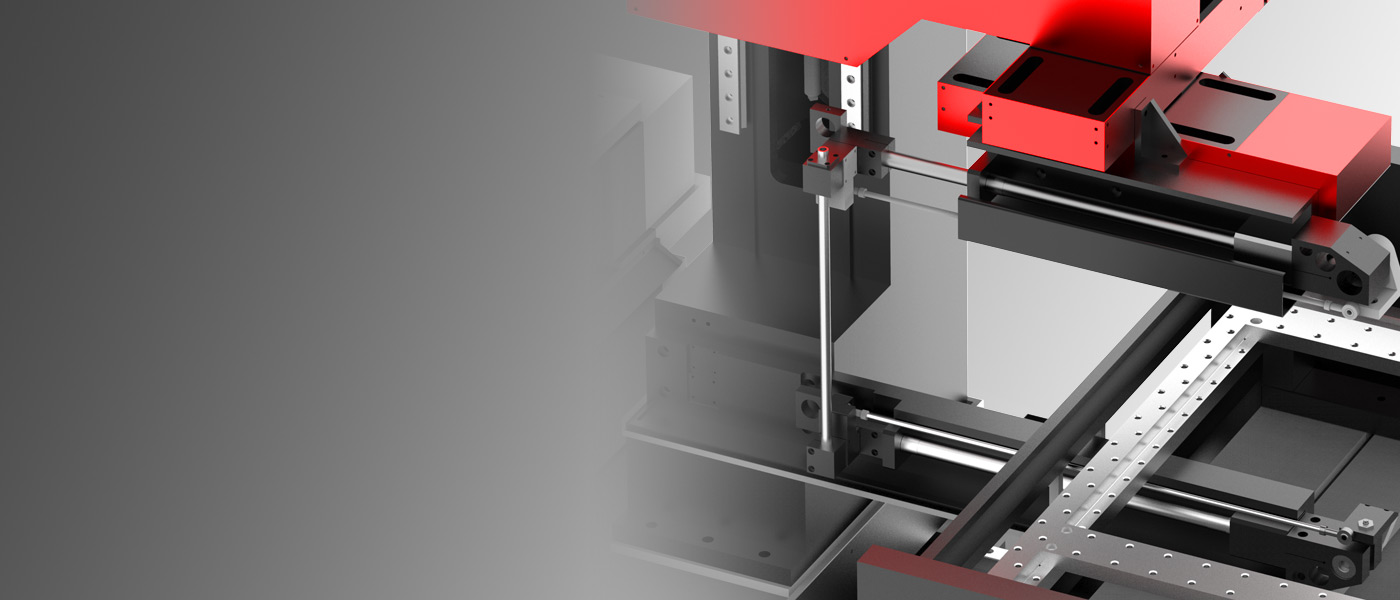
Automatically calculate adjustment.
Automatically adjust upper and lower arm angle.
Automatically calculate adjustment.
3、Z-axis all travel double guideways
The guideway support design is more stable for up and down movement. Taper cut precision, convenient movement.
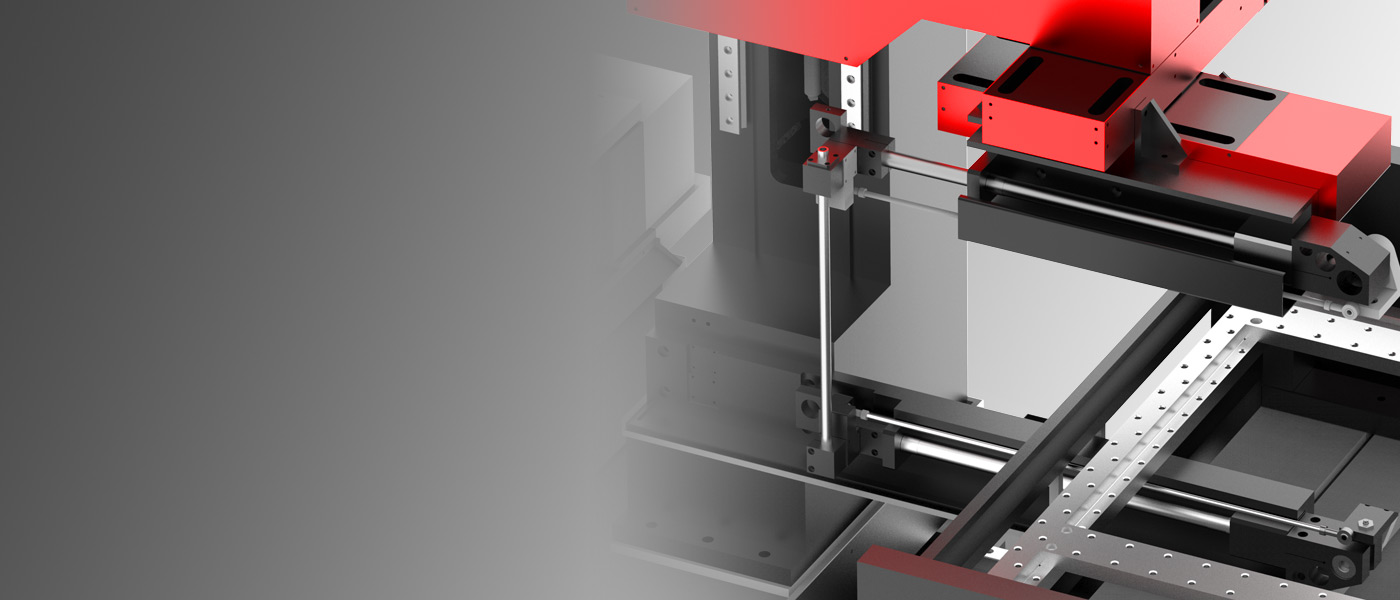
Z-axis double guide way support.
Big taper machining ensures better finish surface and precision.
Promote stability of taper machining.
4、Flexible manufacturing custom
Y-axis could be flexible manufacturing by needs, its max travel reaches 2.6m.
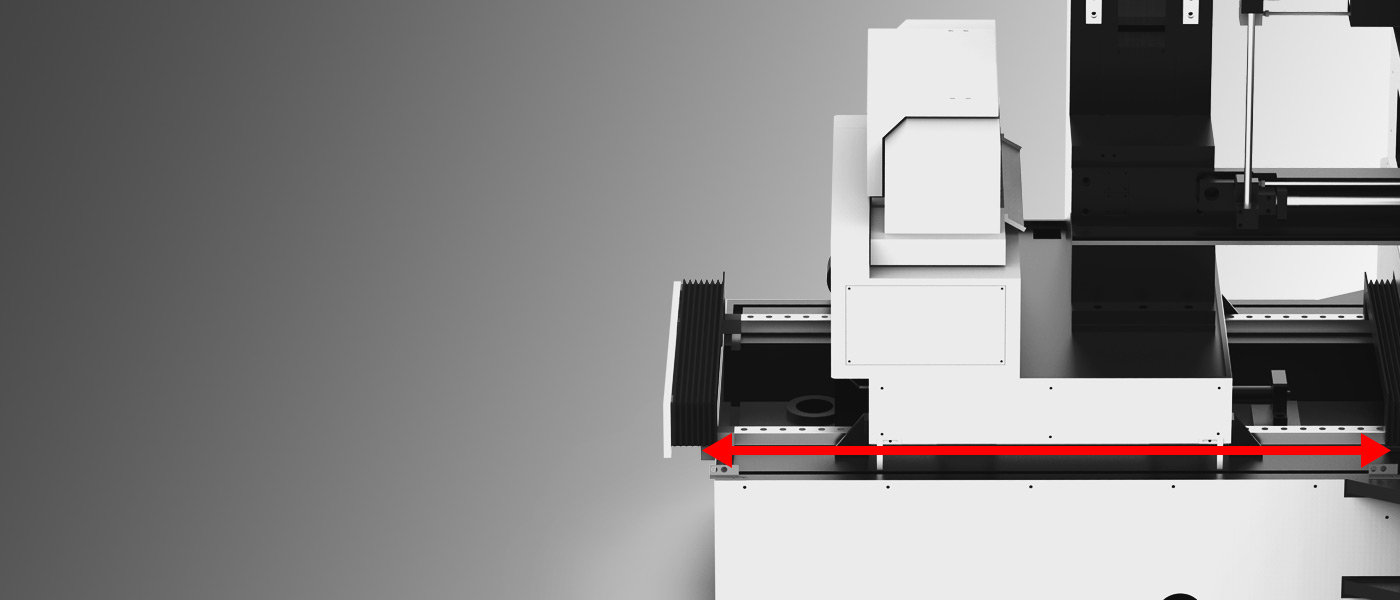
Customized Y-axis.
Satisfy individual manufacturing needs.
Realize large/heavy machining requires.
5、Servo Motor Drive Absolute Encoder
X/Y-axes of ZL series apply servo motor drive to realize high-precision machining, with stability high-speed response and absolute encoder position precision.
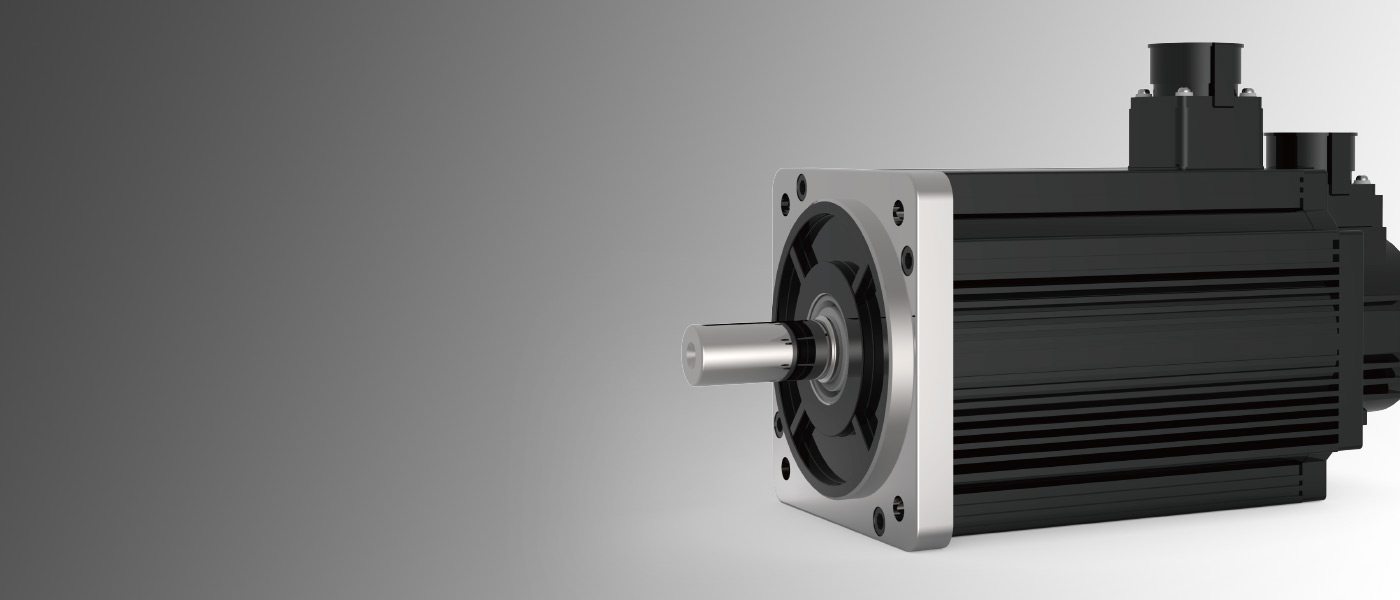
Quick response instruct under the heavy-load.
Specially customize R&D super large moment of torque servo motor.
Super large moment of torque improves machining efficiency.
6、PLC control super-low fault rate
Machine control system uses PLC control model that has high stability, low fault rate, high expansibility, and accommodates industry environment. PLC fits special machining by depth R&D.
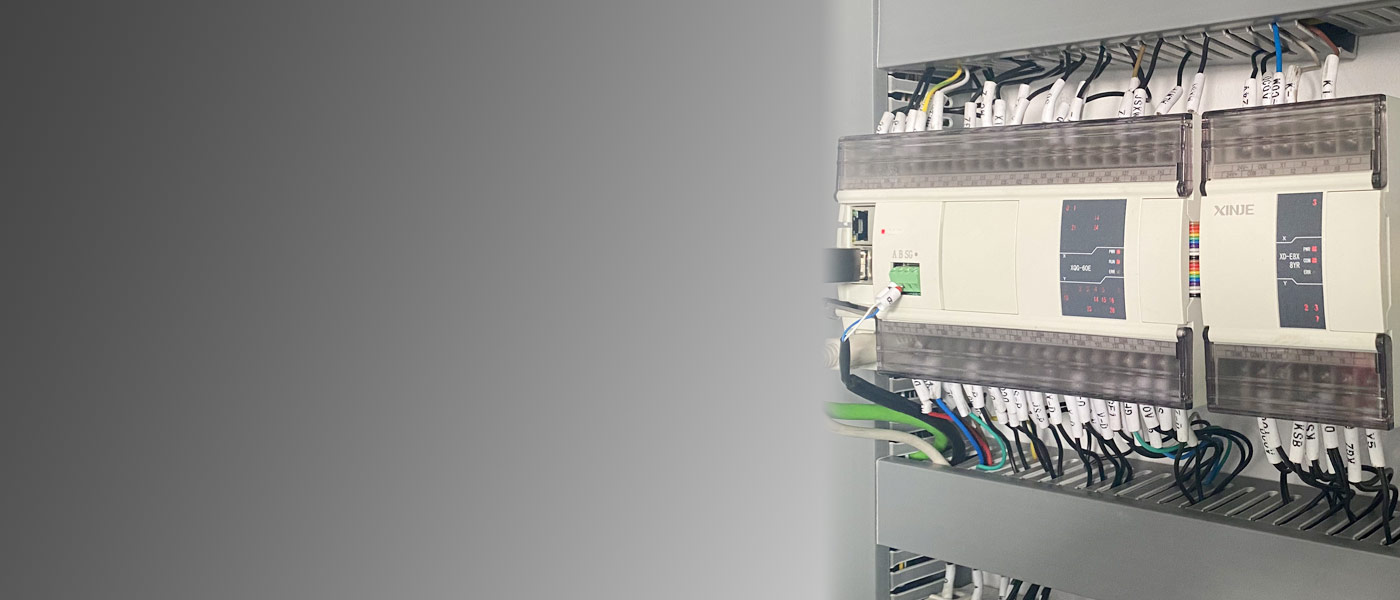
PLC independent Central Processing Unit data instruction response more timely.
PLC super-strong stability, adapt complex manufacturing environment.
Super-strong expansibility, realize future upgrade or flexible customization.
Upper computer network transmission,more stable signal.
7、6-axis CNC
The X, Y, U, V, Z, and wire feed axes are fully CNC, with higher jumping precision, convenient operation, and more accurate position and control.
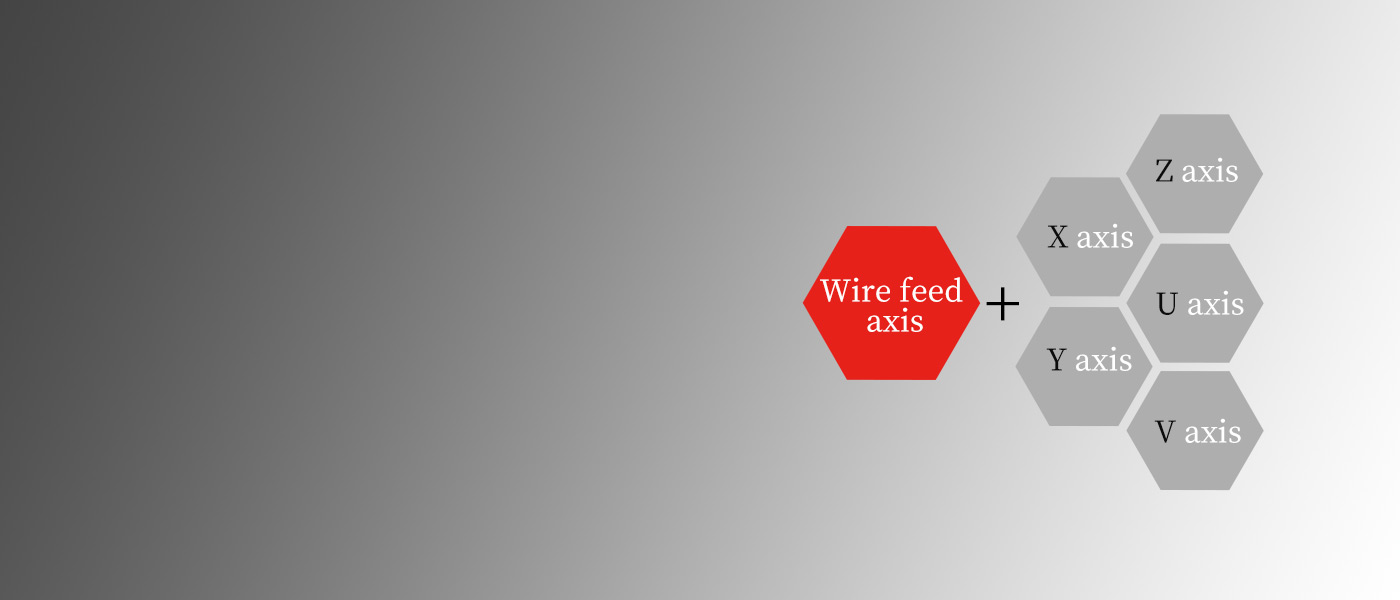
Achieve it in one step.
CNC operation more precisive.
Automatically working.
Achieve it in one stepNo need people to control.
1、Casting
Based on H250 international standard casting, Kingred developed metal ratio to improve casting rigidity and extensibility. All casting passed two times tempering and 3-6 months of natural aging treatment to release inner stress and decrease deformation.
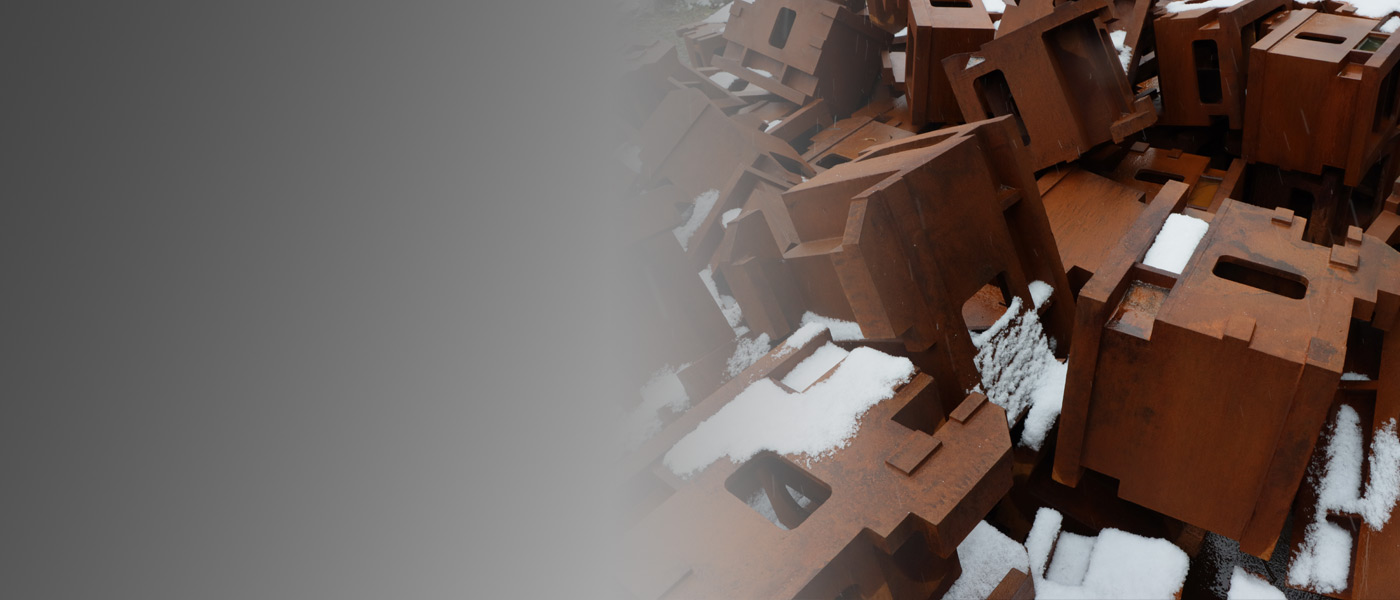
H250 material + Unique rear metal.
Two times tempering/Natural aging treatment vibration aging.
Thoroughly remove internal stress.
High rigidity and stability.
2、Guideway
Sliver 1.5µm SP grade linear guideway realized high precisive position and repeated position to ensure machine height machining stability and precision, load rigidity.
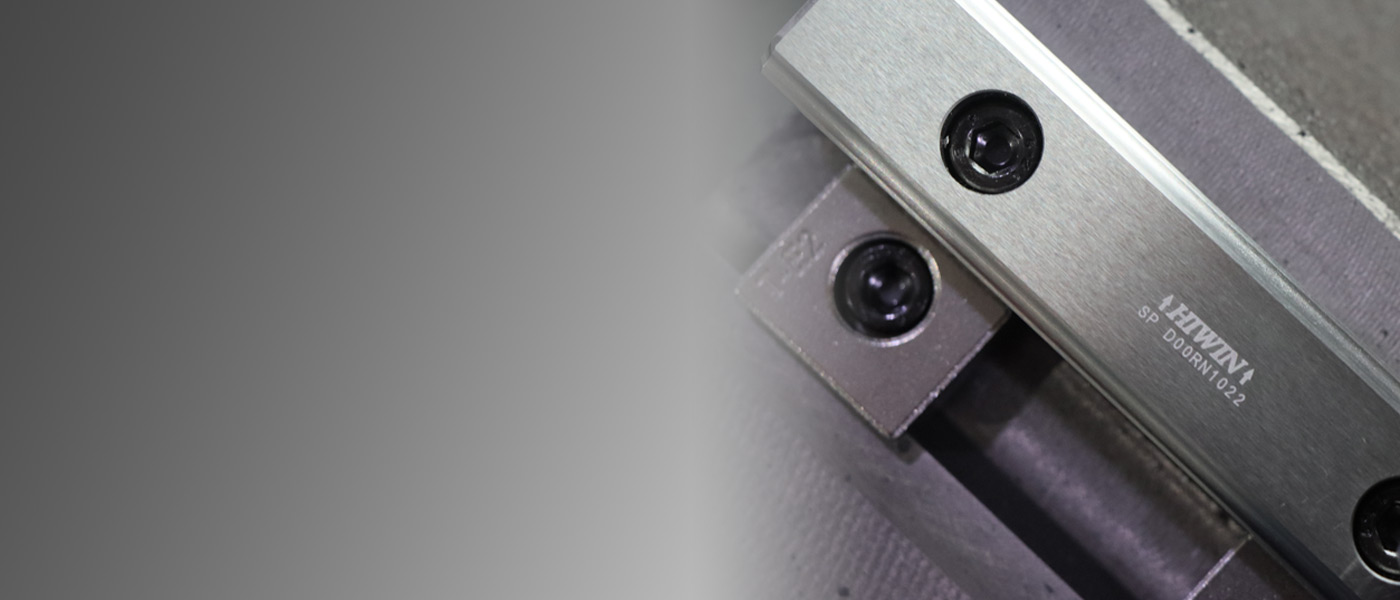
1.5µm super precision.
Super stability and precision machining.
High-load rigidity.
Ultra-precision guideway.
3、Ball screw
P grade ball screw, high-precision ball screw could realize high-precision movement and low friction rate to improve machining efficiency.
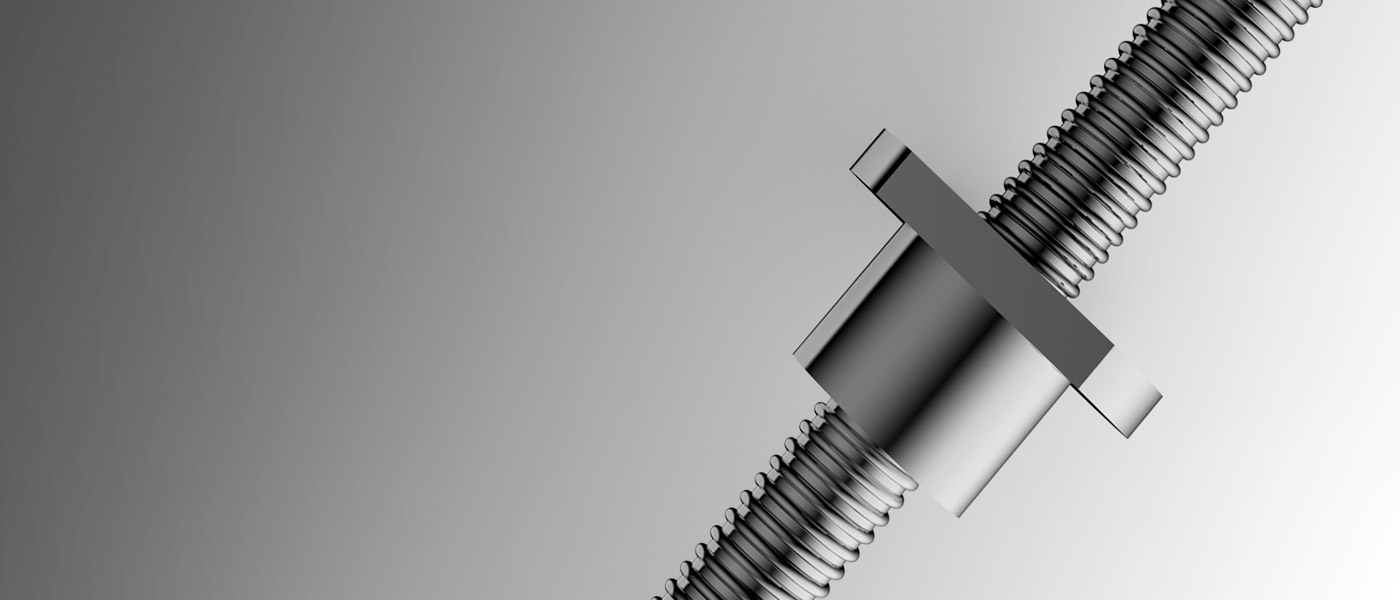
P grade ball screw.
Nan craft P grade ball screw.
High-precision movement.
Extremely low friction coefficient.
4、K-Cut series software intelligent manufacturing
Kingred built ecologically intelligent manufacturing chain, integrating three software K-Cut EDM system, ''K-Cut Wire'' management system, K-Cut PLC system to create a future.
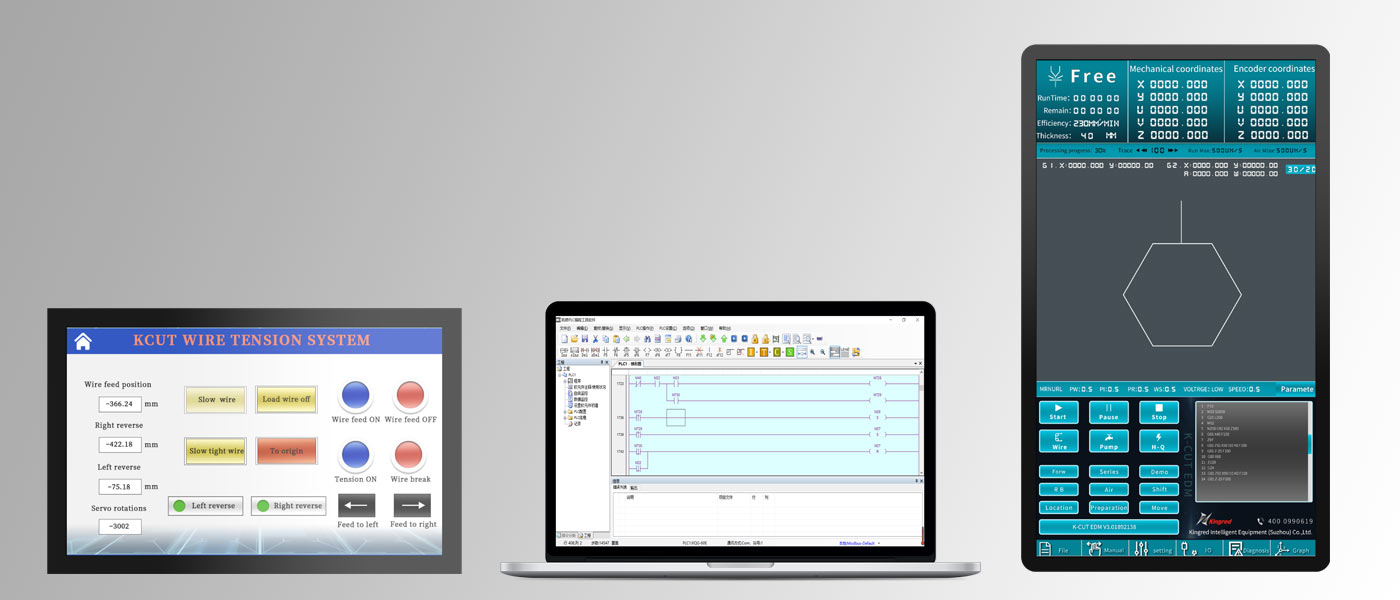
Kingred built ecological intelligent manufacturing chain, integrating three software K-Cut EDM system, ''K-Cut Wire'' management system, K-Cut PLC system.
5、K-Cut EDM system
K-Cut EDM is Kingred independently produced Wire Cut machining system. Graphical drives program, easy to operate. AR Measurement of Slant Edge, Finding the center of a circle, Compensation of Screw Pitch and other practical functions could improve operation. Inside intelligent auxiliary calculation is convenient to calculate kinds of machine deformation.

Self-production copyright, continuous upgrade.
Simple operation to decrease technician training cost.
Kinds of inside practical functions,ntelligent auxiliary calculation,ERP interfaces and remote management integration.
Multi-axis simultaneous machining to achieve complex workpiece manufacturing for taper, variable cone, upper and lower special-shaped.
6、K-cut WIRE system
K-cut WIRE system is an important part of Kingred K-Cut software ecology, which is responsible for wire feed system management. By combining hardware machine structure, it could realize wire digital management and kinds of feeding wire ways to reach convenience.
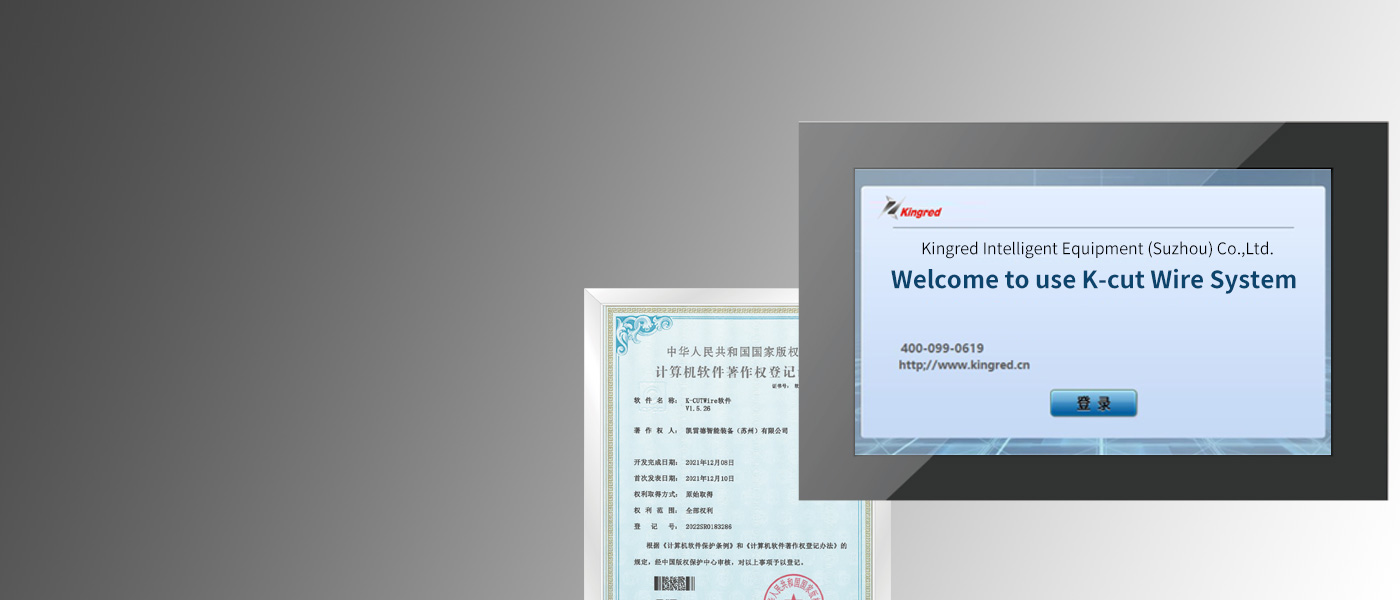
Wire visual data management.
Integrated one-key wire feeding, CNC wire tightening, digital reverse control, wire speed dynamic control.
Wire feed management takes the lead in realizing a new era of digital control and one-key convenient operation.
7、K-cut PLC system
K-cut PLC system is next next-generation intelligent manufacturing expander base, which is Kingred switch to PLC. All series of products applied PLC to replace traditional device. PLC digital processing program has high stability, low fault rate, high compatibility, and scalability, which is a key to keep creation.
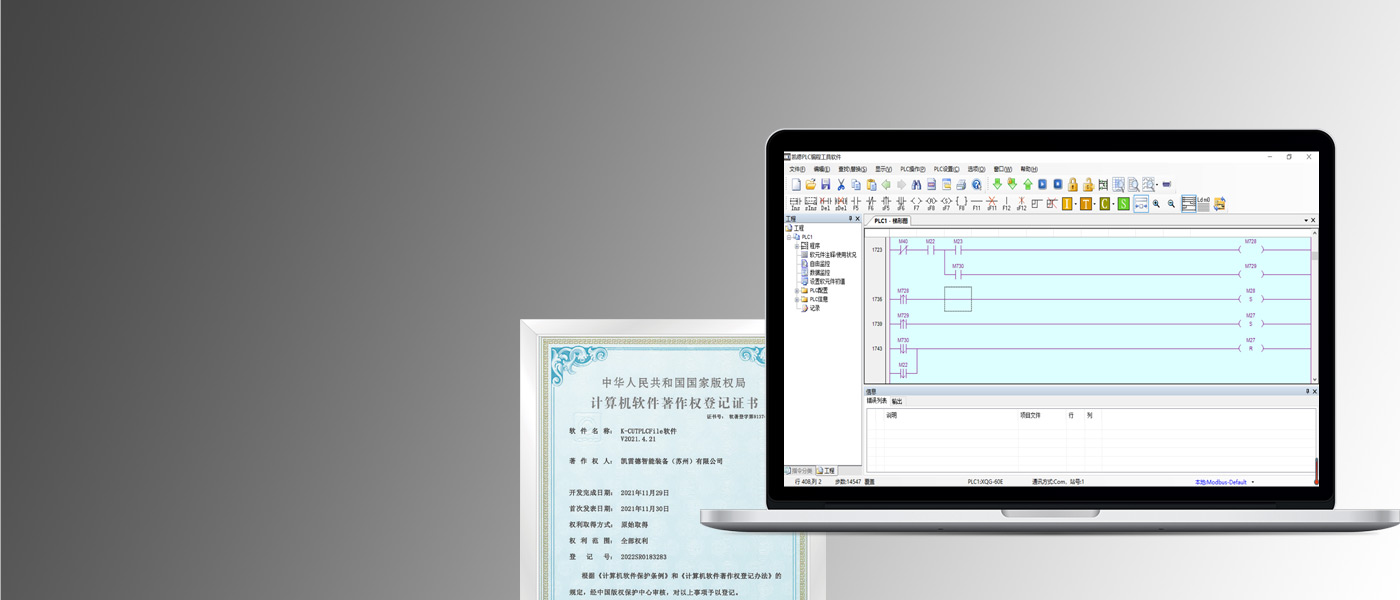
Customized R&D for wire cutting special manufacturing.
Flexible manufacturing customization.
Prepare for next-generation manufacturing interface.
Intelligent manufacturing control entrance.
1、Whole process manufacturing chain
Kingred builds complete manufacturing chain, have perfect manufacturing chain for machining(rough finish, finishing, superfinishing),precise assembly, electric engineering, machine debugging,and process engineering, and realizes to independently finish from part to complete machine. Quality is run through each manufacturing process, builds three system of quality trace for people, product,process, and ensure the stability and consistency of product.
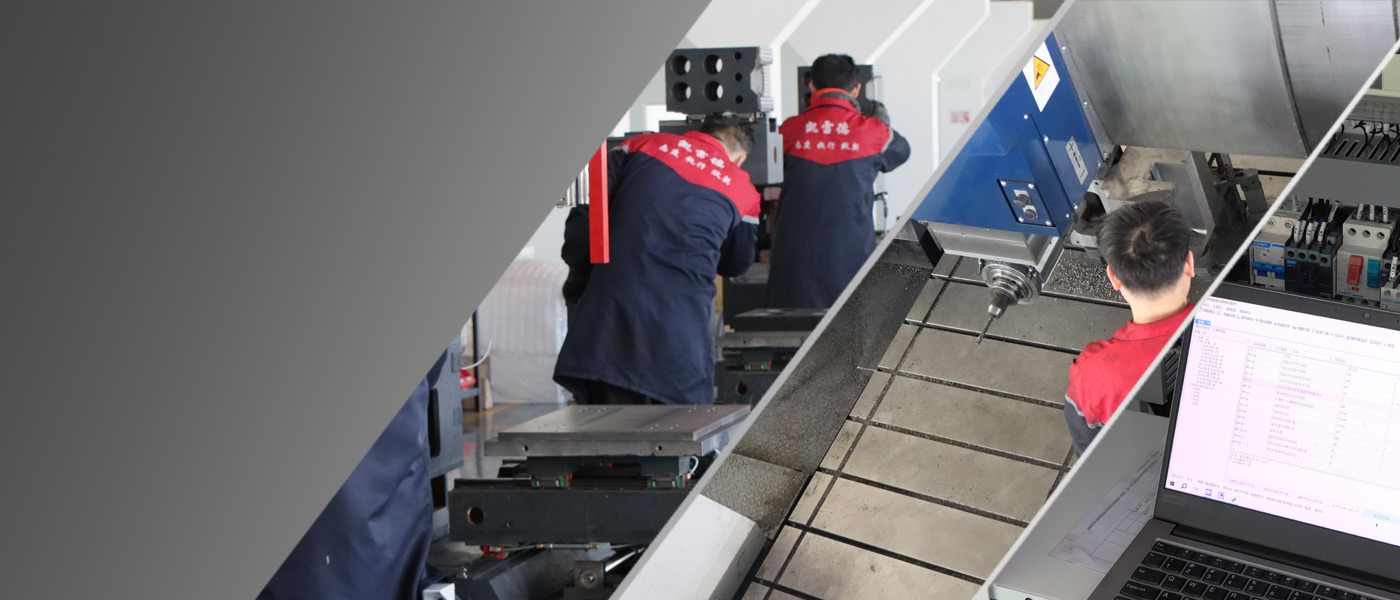
Machining
Precise assembly
Electric engineering
Process engineering
2、Advanced manufacturing equipment
Kingred continually completes and innovates the infrastructure of manufacturing equipment, ensures that hardware is high precision, successively introduces an advanced industry machine for Mitsubishi 5-axis machining center, SNK machining center, DMG machining center, OKAMOTO grinding machine.Industry lead manufacturing hardware equipment is basic guarantee that Kindred's machine has high precision and best surface finish manufacturing.
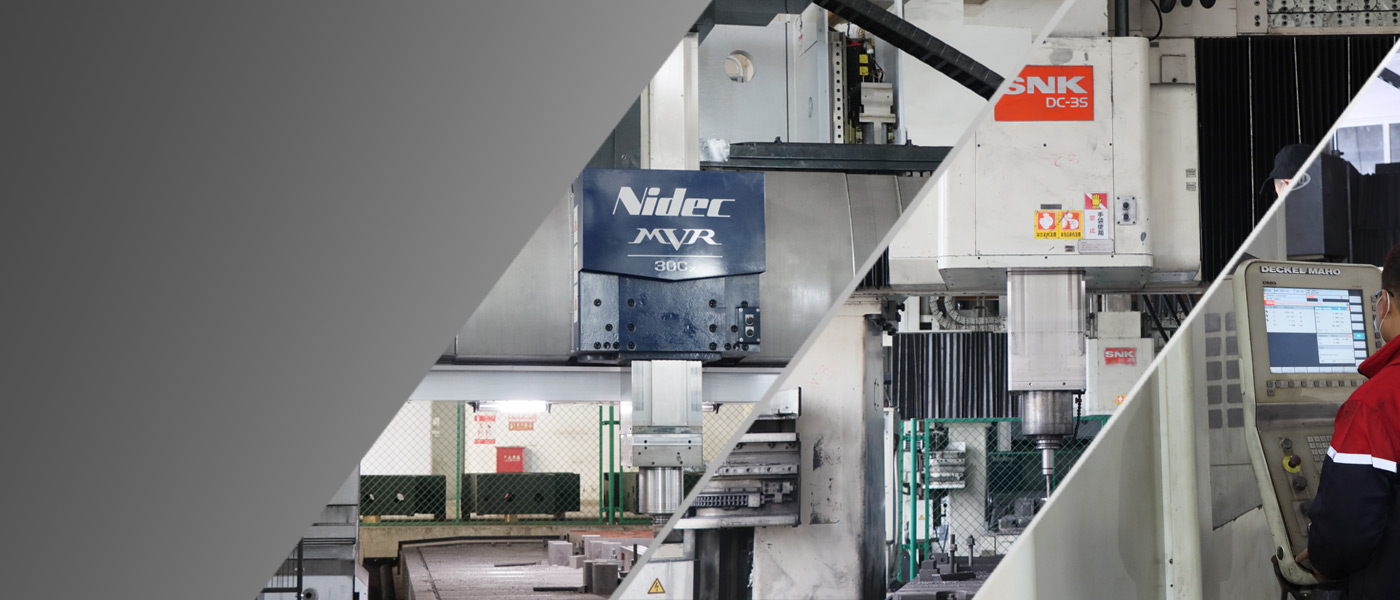
Mitsubishi 5-axis machining center
SNK machining center
OKAMOTO grinding machine
DMG machining center
3、Precise measuring equipment
Kingred have double inspection for manufacturing process and outcome, high precision measuring equipment for API laser inferterometer, Switzerland TEST three-coordinate detector, Germany Planolith marble square, Japan Sanfeng roughness tester,etc realizes from part precision to machine dynamic precision, positional precision and precise test of manufacturing outcome.
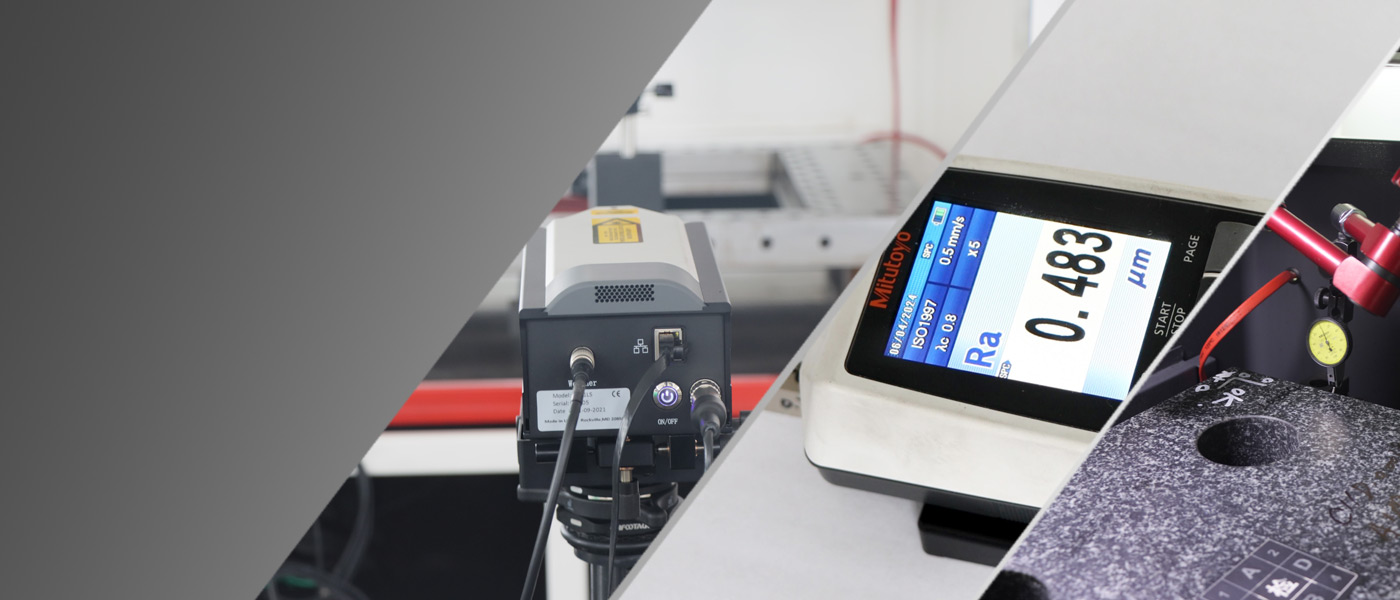
Laser interferometer
Toughness tester
Double zero-grade marble ruler
Three-coordinate tester
4、Ingenuity manufacturing process
Kingred with 17-year manufacturing experience have some experienced manufacturing engineers that working age over 5 years. Keep on connecting traditional craft and modern precise equipment manufacturing, the key high-precision parts adhere to the manual scraping process to ensure that the machine has a stable step distance machining precision for many years.At the same time, the human-centered quality traceability system creates an ingenious manufacturing process.
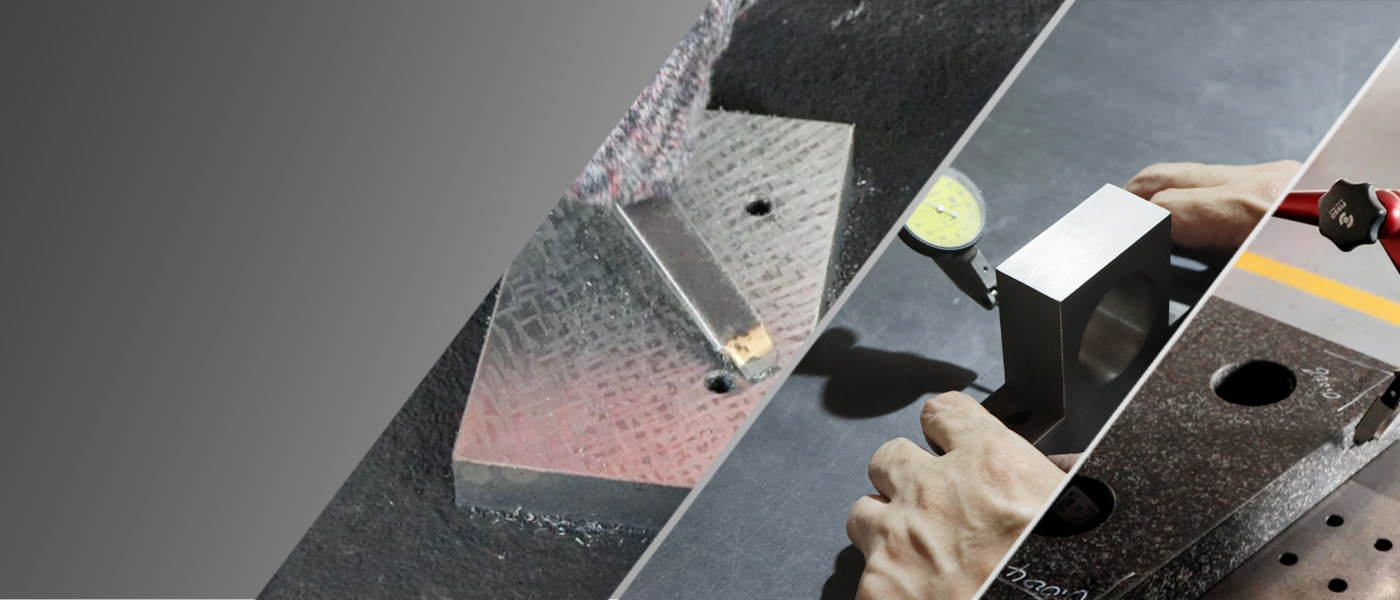
17-year manufacturing experience
Traditional technology application
Quality traceability system
-
Linear Motor Drive Wire Cut EDM KD400L
-
Kingred Precision CNC WEDM KD400ZL
-
High Cutting Speed Wire Cut EDM KD400LY
Customers make us achievement
We will create value for you
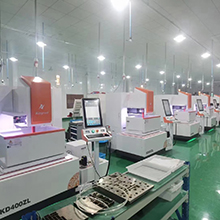
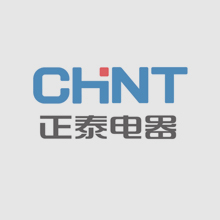
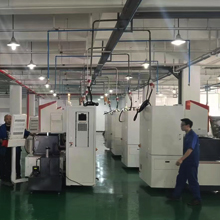
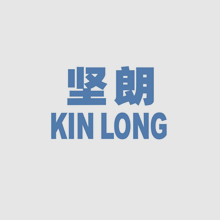
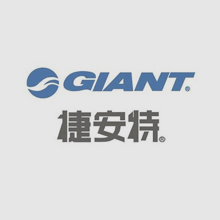
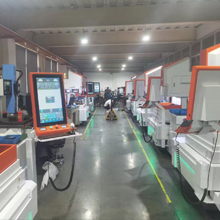
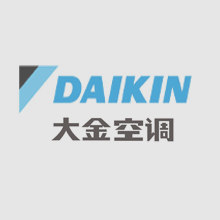
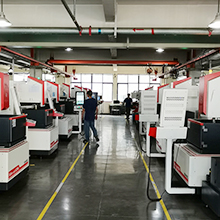